Clean Coal Technology

Development of a catalyst for integrated gasification fuel cells (IGFCs), Elucidation of the chemistry of hetero-elements, Construction of a high-temperature gas cleaning method, and Establishment of a coking technology for poor-quality and unused carbon resources
The Ministry of Economy, Trade, and Industry announced the policy of gradually discontinuing and abolishing old coal-fired power plants that emit large amounts of CO2 by FY2030, while permitting the establishment of new coal-fired power plants that exhibit excellent environmental performances (July 3, 2020). Integrated gasification fuel cell (IGFC) technology, which combines coal gasification and fuel cells, is a promising next-generation power generation methodology that can reduce CO2 emissions by more than 30%, relative to the existing laws and regulations, because it can achieve high power generation efficiency. Based on this perspective, our laboratory has been working on developing a highly active catalyst for use in IGFCs. We are also analyzing the behavior of hetero-compounds, including HCl, H2S, and NH3, present in trace amounts in the generated fuel gases (main components: H2 and CO) and establishing a high-temperature removal system for such compounds (WO2005-162988, WO2015-024400). Moreover, we are developing methods for producing high-strength coke from poor-quality and unused carbon resources, based on organic resource and computational chemistry.
Electrostatic potential map of low-grade coal doped with Na+ cations
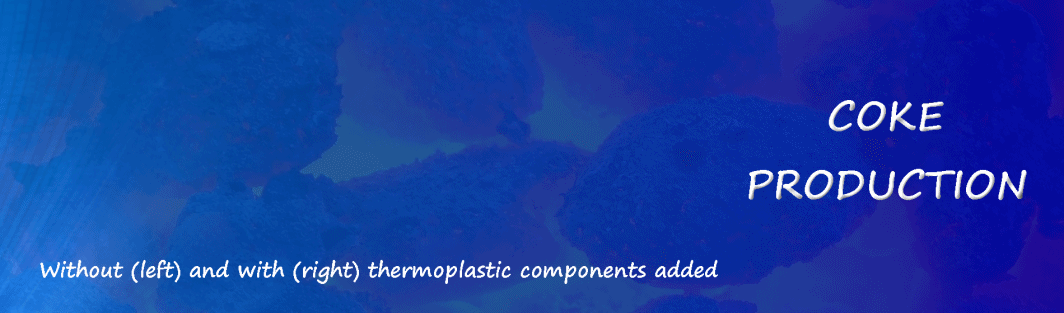
Coking behavior of coal: Left, raw coal and right, coal with added softening and melting components
Environmentally-Friendly Ironmaking Process
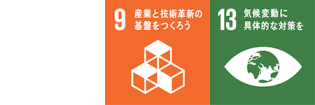
Development of a method for upgrading low-grade iron ores, Production of carbon-containing ores using chemical vapor filtration, Elucidation of the behavior of mercury compound generation and establishment of an emission control method, and Construction of a selective separation and recovery technology of phosphorus in steelmaking slag
As is well known, iron is one of the key materials supporting the modern day society. Currently, Japan is 100% reliant on imports, mainly (90%) from Australia and Brazil, to obtain iron ores (the main raw material of iron). Furthermore, with the rise in impurity levels, the iron content in ores is expected to decrease (deteriorate) in the future. This would lead to increased energy consumption during the ironmaking process, increased CO2 emissions, and reduced productivity. Thus, our laboratory is working on the development of a low-grade iron ore upgrading process using alkali treatment (NEDO Project) and the manufacturing of carbon-containing ores using chemical vapor filtration (NEDO Project, WO2017-193742). We are also promoting the development of a method for controlling mercury compound emissions related to ironmaking processes and a method for the selective recovery of phosphorus from steelmaking slag.
Elemental mapping of carbon-containing ores produced by chemical vapor filtration
Carbon Recycle

Development of a carbon recycling power generation system, and Design of a CO2 conversion catalyst using quantum chemical calculations
In this research, our biggest objective is to simultaneously solve three problems: resource, energy, and the environment. With this in mind we are aiming to develop a carbon recycling power generation system that uses poor-quality and unused carbon resources, such as biomass, as raw materials; has high energy efficiency; and considers CO2 as a resource; and separates and collects it for reuse as a raw material for industrial processes and catalysts. In this system, water-soluble metal cations are added to biomass and brown coal and converted to fuels with high gasification reactivity by the self-replacement effect. This fuel is then gasified in the cells of the molten carbonate fuel cell. Thus, the H2 and CO2 gases are circulated in the cell, with excess CO2 being concentrated on the electrode side, absorbed by hydroxide compounds, and subsequently immobilized. The biggest feature of the system is the reuse of this immobilized CO2 as an added catalyst or raw material in industrial processes. We are also promoting the design and development of CO2 conversion catalysts to convert CO2 originating from large-scale facilities such as thermal power and ironmaking plants.
Logistics image related to a carbon recycling power generation system that uses the self-replacing effect
Aquatic Bioproduction Science
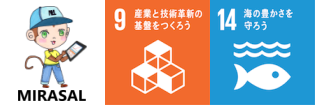
Development of a “visualizing” device to determine when best to eat marine products, and Development and verification of a freshness assessment system for marine products using ITC
In the production and consumption areas of fresh seafood wholesale markets, the freshness of the product is one of the most important criteria for determining the value of the product, and the K value has been proposed as an indicator to evaluate freshness. However, this value is calculated by sampling an arbitrary part of the fish/shellfish after death and performing component analysis after various forms of pre-treatment. Thus, it is not suitable for real-time evaluation in the site of distribution. With this in mind, our laboratory has been developing an evaluation system that predicts the K value based on information such as the size of the product, length of time elapsed after death, and storage temperature (WO2020-037546). Moreover, we are currently developing a system for evaluating freshness of marine products using devices that visualize the best timing of consumption and ICT, jointly with the National Institute of Advanced Industrial Science and Technology (NIST) and Tokyo Denki University.
Social implementation diagram of the results
of our research
JST 新技術説明会資料(2021.9.2)
(CACIKA は MIRASAL の旧名)